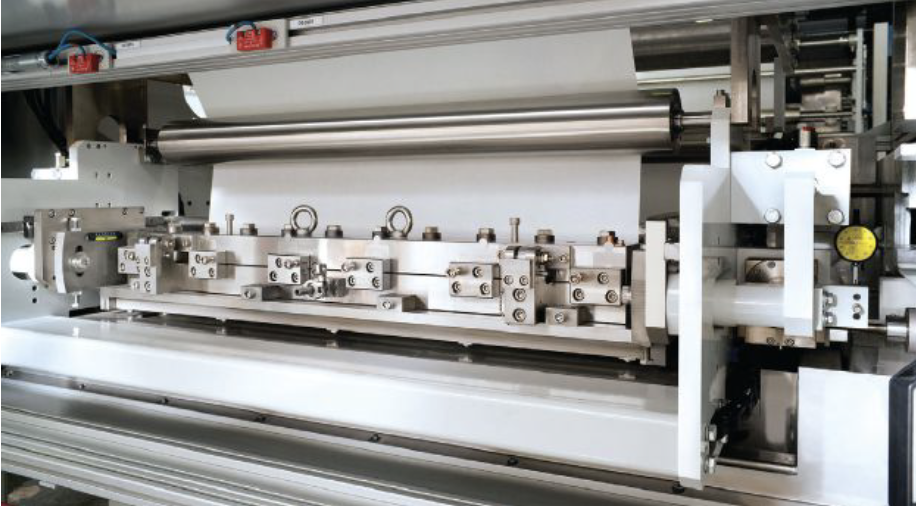
Customized or standardized: Determining what’s best for your battery-manufacturing operation
Converting-equipment manufacturers face a variety of challenges related to customization when designing and building machinery for the energy-storage industry. The need for customization, whether based on emerging technologies for conventional battery materials, such as electrodes and separators
Converting-equipment manufacturers face a variety of challenges related to customization when designing and building machinery for the energy-storage industry. The need for customization, whether based on emerging technologies for conventional battery materials, such as electrodes and separators (or other markets, like polymer membranes, impact protection or recycling), drives lead times in an industry which is changing too quickly to work around a typical equipment-manufacturing cycle. The traditional build cycle for custom equipment designed and manufactured in the USA, coupled with recent supply-chain concerns, begs the question, “How can you build standard equipment for a rapidly growing industry that requires custom solutions?”
This post is for paying members only
SubscribeAlready have an account? Log in